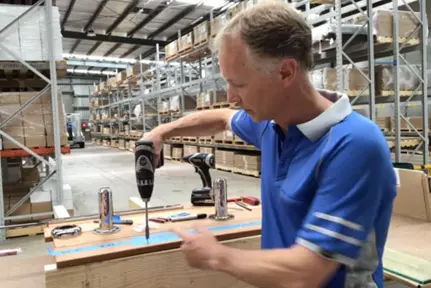
Tips For Installing Flanged or Bolt Down Spigots
Setout
Like everything in building, the old saying “measure twice and cut once” rings true for glass installation, the only problem is that you can’t cut toughened safety glass, so your setout accuracy is crucial to get right.
Masking tape is the installers friend, by using masking tape on the fence line, you can easily see the setout locations on your line, correct mistakes and easily remove all the marks once complete. The tape is an excellent idea on exposed aggregate, concrete, timber decks, tiles and just about any surface you’ll need to mark out on.
Subframe
Make sure your subframe or surface is fit for purpose and robust enough to secure the glass barrier.
If you have a wobbly deck, you’re guaranteed to have a wobbly glass fence. Rotten timbers or poor-quality carpentry will affect the finished quality of your glass fence or balustrade.
Glass gates are fussy, they will punish a poorly built deck, the tolerances between panels are very small, and any movement on a deck will affect the performance and safety of a glass gate.
Especially for pool fences where safety is vitally important, a quality built subframe will give glass gates many years of maintenance-free operation, of course, you’ll still need to perform an annual safety check to ensure hinges and latches have any adjustments required.
Use the right fixings
It doesn’t matter how strong the glass and spigots are if you don’t use the correct fixings, the glass barrier has to be securely fastened to the subframe, you cannot rely on just fixing to the decking boards.
The fixings or screws that secure the fence or balustrade must have deep embedment into the sub-frame to ensure a sound attachment that will last.
Stainless steel fixings are the preferred method with galvanized screws coming in second place.
Tip – Easy Installation of Glass Fencing and Balustrade into Spigots
An easy way to insert the glass panels into flanged spigots is to use the plastic safety corners supplied with each panel of glass, use the plastic corner to hold open the plastic insert and just slide in the glass.
Drilling holes – Timber
Drilling holes in timber decks are easy if you follow a few tips to ensure you don’t split deck boards.
Use a 10 or 12mm spade bit to drill a clearance hole through the decking board, this hole is bigger than the screws used, so there is no risk of slitting a deck board. The added benefit is that the sharp point on the spade bit gives you a centering position for the fixing to follow and the sharp center point also allows very accurate drill placement.
Drilling holes – Tiles and pavers on concrete
Drilling holes in tiles take a little longer but ensure you won’t crack a tile or paver if you follow these tips:
Masonry fixing to tiles on concrete – a clearance hole larger than the fixing is required to prevent the Dynabolt or sleeve anchor from binding on the tile and cracking the tile once the nut on the fixing is tight. A simple method is to use a small 10 or 12mm diamond tile drill to cut a clearance hole first then you can drill into the concrete substrate without risk of tile damage.
Making a template from a piece of plywood with a rubber backing glued in place with contact adhesive, mark out the holes for the spigots in the template and pre-drill those with a spade bit. Make the template big enough so you can stand on the plywood to hold it securely in place and drill the clearance holes.
Once you have marked out the spigot and hole locations, you can use the template to drill out each of the holes using a cordless drill, diamond bit and a water spray bottle.
Drilling holes – Plain and exposed aggregate concrete
Drilling holes in concrete takes more time and some extra attention to detail.
Use masking tape to set out the fence line, and this will ensure easy to read markings and better accuracy, especially on exposed aggregate as it is tough to mark out and see your spigot locations.
Use a small masonry bit for the first, 3 or 4mm is ideal as its much easier to be accurate in the drill location with a small drill bit than the final size up to 10mm. Using a template board that you can stand on is also helpful to get accurate holes for the spigots.
Drilling holes – Tiles on compressed cement sheet
Where spigot installation occurs on tiles that will be installed on a compressed cement sheet on balconies that comprise a waterproofing system, we do not recommend installation after tiling.
By penetrating the waterproofing by drilling through the tiles, the waterproofing system has been compromised and will leak over time.
The only safe way to install on a tiled balcony that has a physical water barrier is to install the spigots before the waterproofing and tiling.
Once the compressed cement sheet has been installed, and suitable subframe provision has been allowed for the spigots to be securely fixed to, the spigots can be installed.
After spigot installation, the waterproofing contractor can apply the barrier to the balcony sealing the spigots as part of the waterproofing.
The tiler can now tile the balcony and cut tiles around the spigots. Once the tiler has grouted and sealed the tiles the spigot cover rings can be installed and glass inserted to the spigots.
Spigot rotation
The single most significant factor in installation error and glass failure is the incorrect installation of the spigots. The reason glass fails is the spigots are twisted and create a sharp pressure point on the glass, over time this could result in the glass panels breaking.
The simplest way to overcome this risk is ensuring the spigots are perfectly aligned for the glass.
By using a straight edge in the spigots placed into to the glass slot and clamping the straight edge in place with the clamping screws you’ll get a perfectly straight line of glass with no risk of failure. A cheap and straightforward straight edge is a 12mm thick piece of skirting or architrave from your local hardware store.
Step 1
Pre-drill all spigot clearance holes (for timber decks) or in concrete the final holes, place the spigots in location and insert the fixings but leaving them 2-3mm above the spigot to allow some movement.
Step 2
Insert a straight edge into the glass slot and tighten the grub screws of the spigot, by tightening the screws the spigot will rotate to be in a straight line, ensure the spigots are in line with the center of the fence line.
Step 3
Tighten all of the fixings for the spigots and slide the straight edge along to the next spigots and repeat.
Adjusting height or level differences
Our flanged spigots come with 1mm levelling packers, these small black packers are used to adjust the height of the glass. To install the packers, loosen the spigot clamping screws and lift the glass panel, place the packer directly under the glass to raise the height of the panel.

Download this free pool fence guide now
Read On
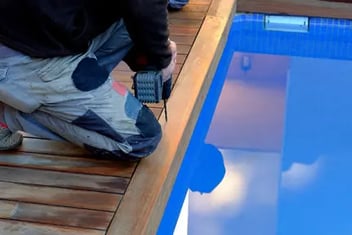
Tools required for glass pool fence and glass balustrade installation - Exakt Glass
The tools required for glass pool fencing and glass balustrade installation are not specialised,...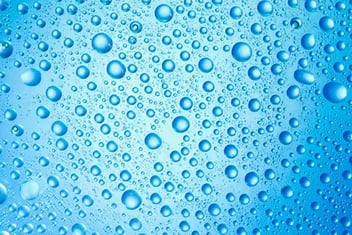